I usually drive to town on P Road past Kinsley Feeders. This past month, I’ve watched truckloads of green fodder being pilled and packed in large hills and then covered with tarps. This is a current method for fermenting and storing silage for winter feeding.
In 2005, I interviewed the late Bill McLean (1916-2007) who lived on a farm not too far from me. Many of you have heard me say that everyone has a story, and Bill told me an amazing one.
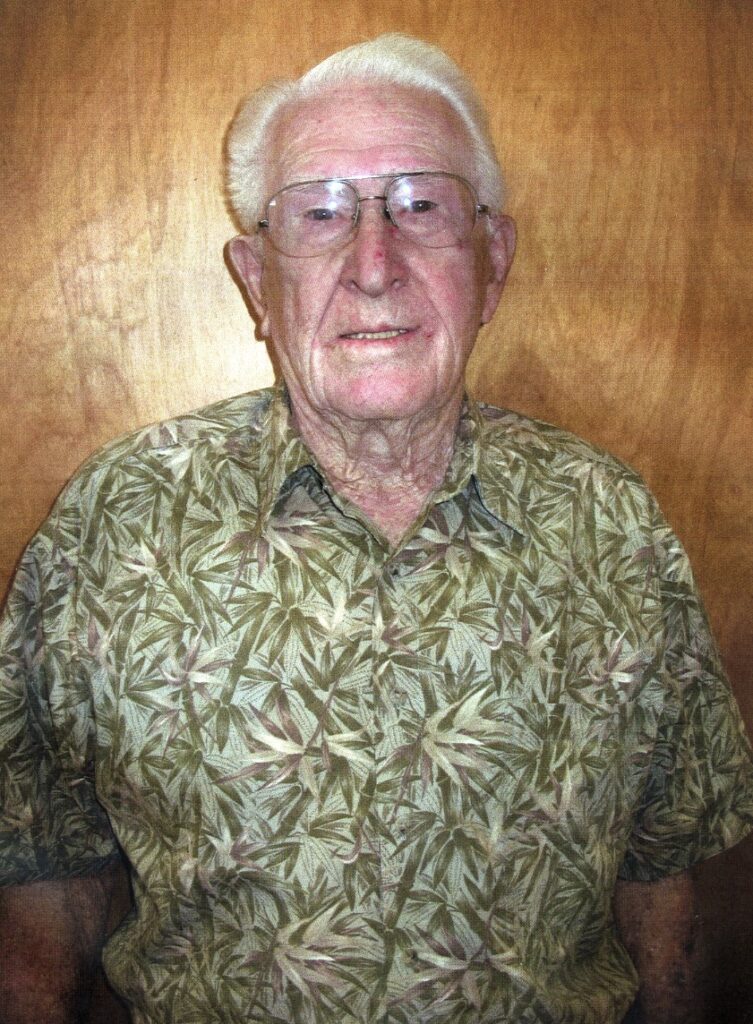
But before I relate it, I’ll share a little history. The word “silo” comes from a Latin word meaning “cellar” because the earliest method of making silage was in a trench or pit. Behind my house, I have two old trench silos dug into the sand hill by the Schaller family. Trench silos often accumulated water which caused mold and spoiled the silage.
So a new method, an upright silo, was developed and became popular in the early 1900s. This familiar farm landmark was built out of wood, manufactured staves, special curved bricks, hollow tile, galvanized iron, or rings of concrete.
Hay or green corn shocks were chopped up and blown into the top of this silo using a flat belt driven cutter powered by a tractor. A farmhand had the hot, dirty job of being inside the silo to direct the stream from the blower and to walk around and pack it down.
Unloading the silage was done by hand by pitching it from the top and down into a wagon or truck below. Winter-frozen silage had to be chopped out with an ax.
Bill McLean grew up on the farm in the 1920s, and he had lots of chores. From a very young age he drove tractor, helped care for the animals, and pitched silage. But he also found time to tinker with building things in the shed. His dad thought this was foolishness, but as long as he had his chores done, he was allowed to do it.
“Necessity is the mother of invention,” Bill told me. When World War II created a shortage of farm workers, Bill saw the necessity of reducing manual labor on the farm.
“The first idea concerning a silo unloader came to me in about 1941 when we were feeding 500 calves by the old fork method. At that time, there was a machine on the market that advertised it could throw out ensilage at a rate of 72 pounds per minute. Feeding 500 calves would take most of the day, so I began to think about various ways of accomplishing the job more easily. Finally deciding that I had the most practical way in mind, I began to pick up parts to start to assemble the first machine. Although things did not always go smoothly, I could see it was going to be the machine for the job.”
Bill gathered old and new parts and got started. It was difficult to get welding equipment into the silo, so when he had to make changes, he had to hoist the machine over the side of the silo and take it back to the work shop to use the electric welder and acetylene torch.
“This first machine had a capacity of about 300 pounds per minute,” Bill continued. “I used a 5-horsepower electric motor. The silo was a 22-foot structure. This model worked to my satisfaction….I decided the machine was patentable and went to a patent attorney. I steadily made improvements until I thought the machine was ready to be manufactured and marketed.”
The unloader was first shown at the State Fair in Hutchinson in September, 1952. It attracted the interest of the Dodson Silo Manufacturing Company in Wichita. Bill formed a corporation with them. More improvements were made to handle all types of silage, and a patent was granted in May, 1954. Soon the Big Boy McLean Silo Unloader was being sold all over the U.S.
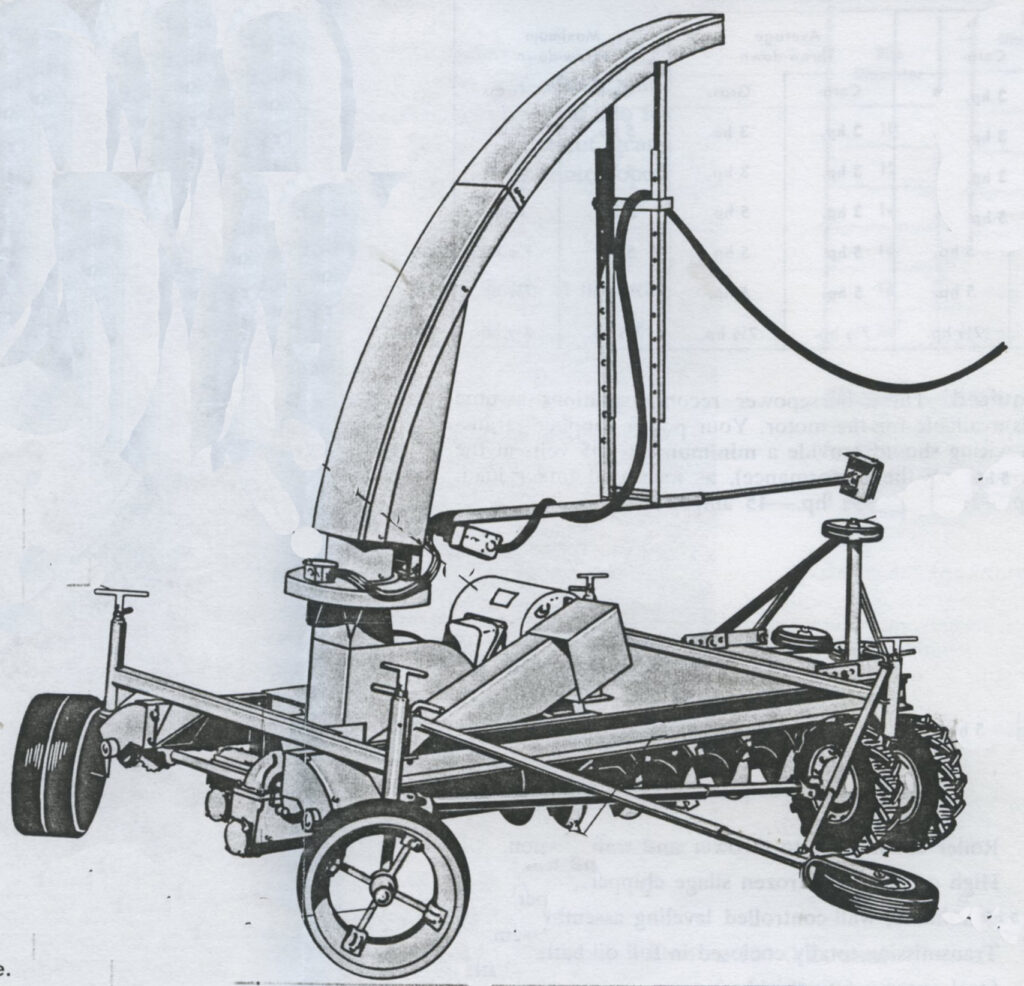
This unloader, which rested on top of the silage, could be adjusted to any size of silo by simply changing the size of the auger. While in operation, it pushed against the inside of the silo walls at the same time drive wheels gave it forward propulsion. As the unit moved around, silage was plowed up by the auger and conveyed to the center of silo where it was kicked into a fan which blew it into a chute. The length of the unit was slightly more than half the diameter of the silo, so all silage was picked up, leaving no mound in the middle. It would eat itself down and around, keeping silage perfectly level until it reached the bottom of the silo.
The unloader worked easily with just one man. It also eliminated lumpy silage and could even shred frozen silage. Bill said, “Install a machine, throw a switch, and you never fork silage again.”
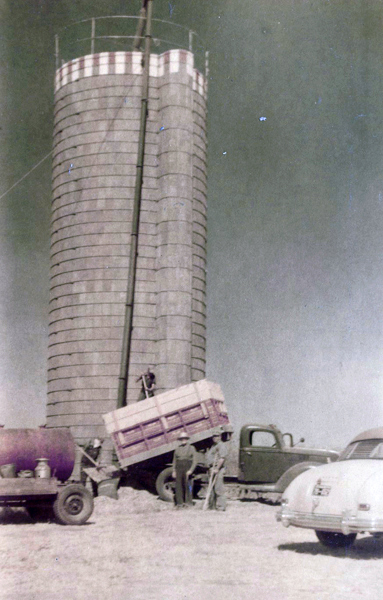
Bill sold the patent to the New Holland Machine Company for $50,000 about 1957 “That was a pretty good chunk,” he said. “It was at the time the girls were getting ready to go to college. That put them through college.”
New Holland flew the whole family to Pennsylvania to sign the contract. Then they supplied them with a car for a two weeks’ vacation in New York City which included the Statue of Liberty and tickets to “My Fair Lady” and the Rockettes.
If you would like to read more about Bill McLean’s life and that trip to NYC, you’ll find it along with 82 other amazing life stories within the library’s oral history archive.